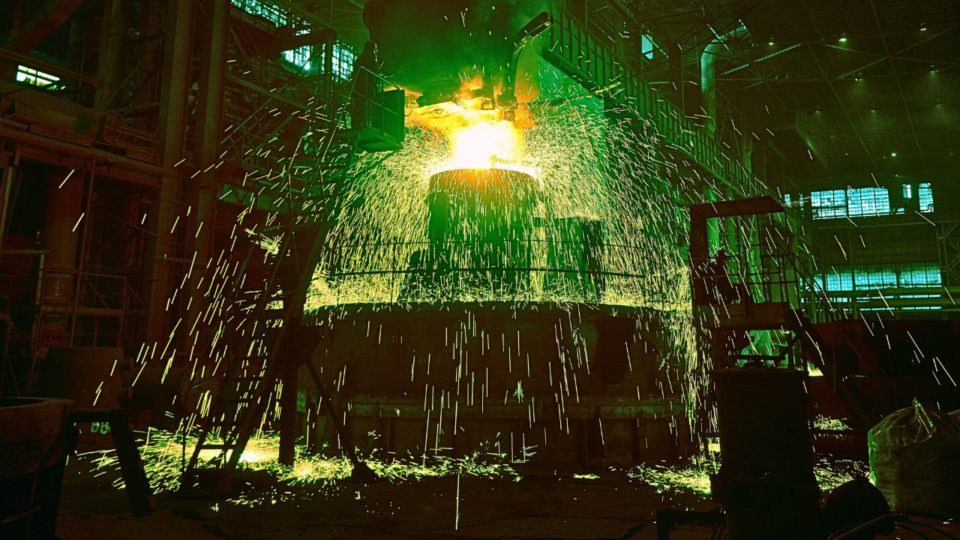
Сталь в нашем мире необходима практически везде. Она используется при постройке зданий и океанских судов, при производстве гаечных ключей и детских игрушек. Во всем мире ежегодно производится почти 2 миллиарда тонн стали и половина из них — первичное сырье. Отрасль несет ответственность за 7%, по другим данным 9%, мировых выбросов углерода. Без снижения эмиссии в этой отрасли промышленности, запланированный во многих странах мира переход к низко- и безуглеродной экономике невозможен.
Однако переход к «зеленой» стали затруднен необходимостью пересмотреть давно отработанные технологии, в которые были вложены даже не десятки — сотни миллиардов долларов. И хотя металлургия сильно отстает в этой сфере от преобразований в области энергетики и транспорта, в которых «зеленый переход» обозначился уже 20 лет назад, за последние десятилетия даже в ней происходят серьезные изменения. Уже сейчас в разработке находятся более 50 перспективных технологий существенно сокращающих выбросы СО2 в металлургической промышленности.
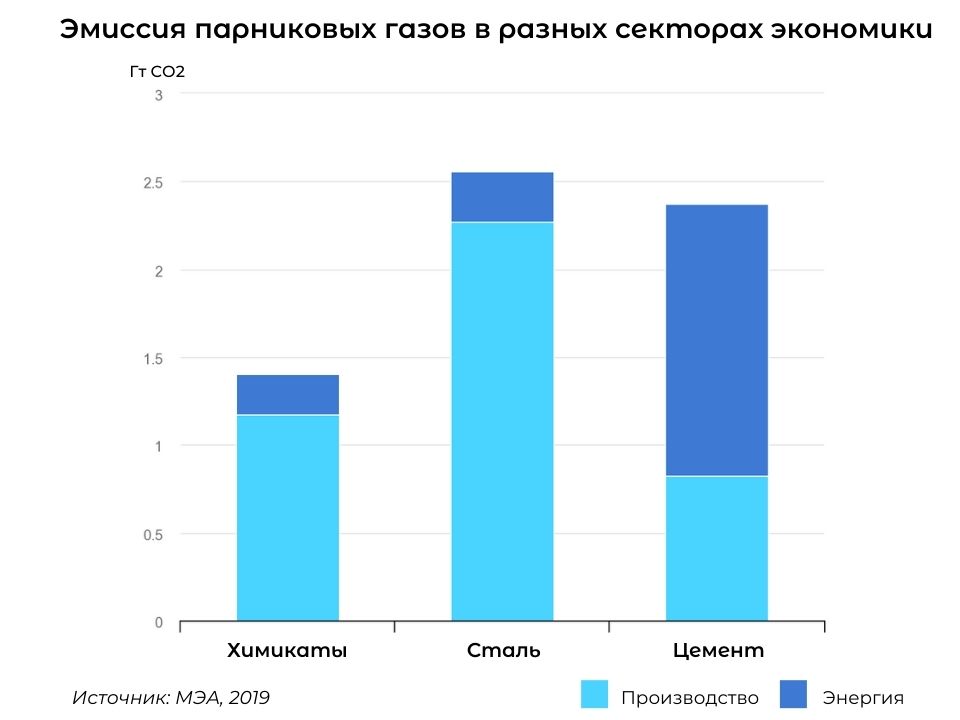
Мартен тормозит процесс
Долгое время металлургия зависела от угля. Даже сейчас потребности в энергии, которая потребляется во время технологических процессах плавки и проката, на 75% обеспечивается углем. Поэтому первый шаг к низкоуглеродному будущему металлургии и сталелитейной промышленности — это электрификация с использованием возобновляемых источников энергии (ВИЭ), переход к электродуговым печам (ЭДП) и радикальное снижение потребления угля, то есть отказ от использования кокса.
Сейчас примерно 70% всей выплавляемой в мире стали производится доменным способом. В таком процессе кокс используется в основном корпусе печи. Частично его можно заменить водородом. Водород будет удалять кислород из руды, образуя воду вместо CO2. Это потребует использование ВИЭ для производства зеленого водорода.
Но есть проблема — по сравнению с коксом при использовании водорода доменной печи требуется больше внешнего дополнительного тепла для поддержания высокой температуры. Что еще более важно, кокс в основном корпусе печи нельзя заменить водородом. Для его замены можно использовать биомассу, смешанную с углем.
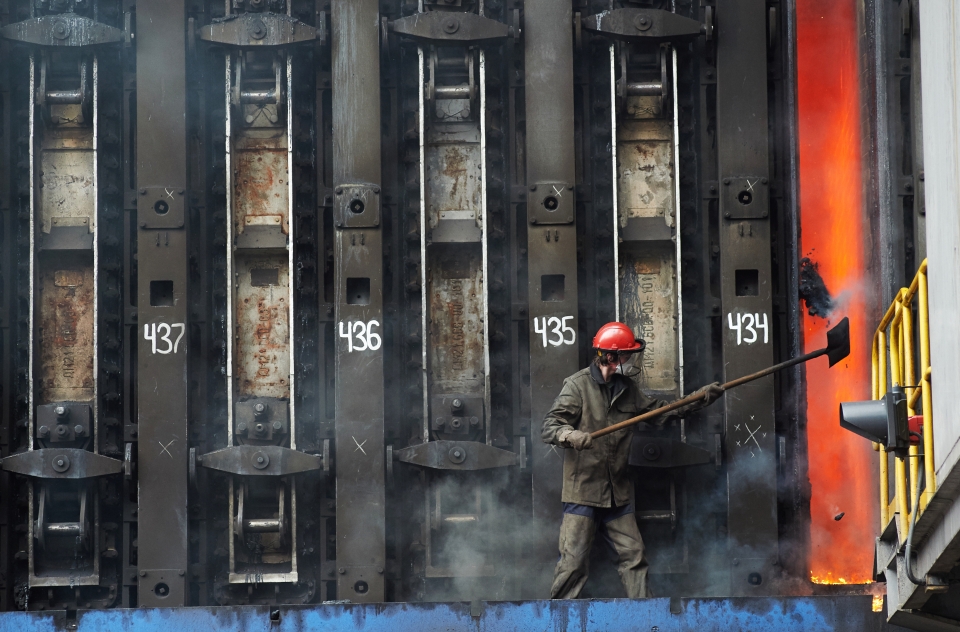
Однако получение биомассы устойчивым образом в больших масштабах — огромная проблема. Проще говоря, у нас нет такого количества лесов и отходов деревообрабатывающего производства, чтобы заменить весь используемый уголь. К тому же, выбросы СО2 будут сохраняться на уровне лишь немногим ниже, чем при использовании кокса. Да и лесовосстановление в данном случае не будет устойчивым, так как потребление стали будет постоянно возрастать. А значит — будет расти потребность в заготавливаемой биомассе.
Чтобы »озеленить» эти процессы, можно использовать технологии захвата и захоронения углерода (CCUS). Однако имеющиеся на данный момент технологии слишком дорогие, и пока не вышли за рамки тестирования.
Поэтому конечным итогом всех технологических преобразований становится замена угля и газа на такие альтернативные источники энергии как водород.
Как работают технологии захвата и хранения углерода: промышленная революция наоборот
Электрификация и вторичная переработка
Фактически, переход на ЭДП требует эффективного использования лома, то есть, вторичной переработки промышленных отходов. С этим есть серьезные проблемы, так как сейчас используется только около 200 млн тонн лома для производства стали. В ближайшие 10-20 лет этот объем можно поднять до 700 млн тонн, но это лишь треть от уже имеющегося уровня производства.
У применения ЭДП есть существенное преимущество — на каждую тонну стали выбрасывается 0,4 тонны СО2. Для сравнения, при использовании мартеновских печей эмиссия составляет 1,5-3 тонны СО2. Причем большая часть выбросов ЭДП образуется из-за использования электроэнергии, которая получена при сжигании ископаемого топлива. То есть это количество можно снизить еще больше, если использовать электричество из возобновляемых источников.
Проблема в том, что по расчетам объем требуемой стали к 2050 году вырастет до 2,6 млрд тонн. Для того, чтобы ее производство было устойчивым, необходимо добиться 80-90% глубины переработки лома, что в несколько раз выше того уровня, который есть сейчас. К тому же, переработанная сталь, как правило, имеет более низкое качество из-за плохой сортировки и проблем с загрязнением побочными продуктами технического процесса — медью, никелем и оловом. Так что растущий спрос на продукцию придется удовлетворять, выплавляя новую сталь из железной руды.
Отказ от кокса со своей стороны требует использования в технологических процессах железа прямого восстановления (DRI). Суть этой технологии — производство железа непосредственно из руды, без использования доменных печей.
Сложность здесь только одна — топливом для этого процесса служит газообразный метан для производства водорода и монооксида углерода, которые затем используются для превращения железной руды в железо. Теоретически это позволяет снизить выбросы СО2 с каждой полученной тонны в два раза, но говорить об »экологичности» такого процесса не приходится.
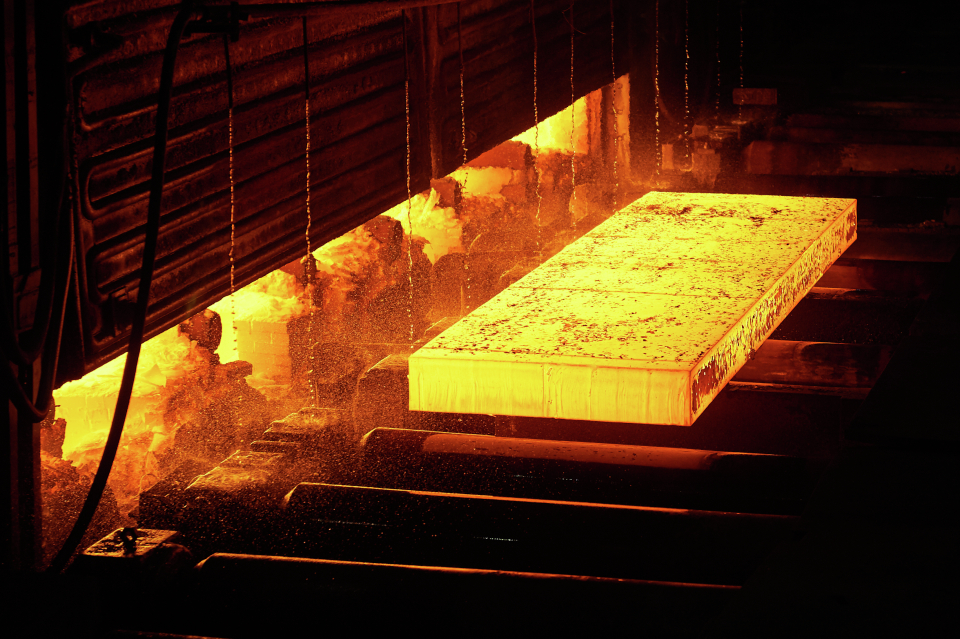
Этот метод требует больше электроэнергии, чем доменная печь. И здесь есть существенный потенциал для сокращения энергозатрат. Пока на эту технологию приходится менее 5% производства стали. Но метод прямого восстановления предлагает наилучшие возможности для использования зеленого водорода, поэтому эта область будет быстро развиваться в ближайшие годы.
До 70% водорода, полученного из метана, уже можно заменить зеленым водородом без необходимости слишком большого изменения производственного процесса. Однако работа по полному переводу DRI на зеленый водород продолжается.
Деньги для ускорения
Все вместе эти меры потребует около 1 трлн долларов инвестиций в металлургическую промышленность до 2050 года. А по расчетам европейских исследователей в ближайшие годы ЕС потребуется 50-60 млрд евро инвестиций и около 120 млрд евро ежегодных расходов на операционную деятельность.
По прогнозам Международного энергетического агентства (МЭА) новые технологии должны внедряться очень быстрыми темпами, чтобы выполнить намеченные цели по снижению выбросов на 50% к 2050 году. Требуется вводить по одной водородной установке DRI в месяц после выхода технологии на рынок.
По расчетам, это повысит спрос на электроэнергию на 720 тераватт-часов к 2050 году, что эквивалентно 60% общего потребления электроэнергии на данный момент в металлургическом секторе. Одновременное развертывание установок, оборудованных CCUS, требует улавливания около 0,4 Гт CO2 во всем мире в 2050 году. Это означает развертывание крупной установки CCUS (улавливание 1 миллиона тонн CO2 в год) каждые 2-3 недели, начиная с 2030 года.
Между тем ситуация по внедрению новых технологий в настоящий момент далека от таких темпов. Больше 2/3 проектов по внедрению технологий производства »зеленой» стали сосредоточено в Европе. В Индии, которая к 2030 году будет производить 20% стали в мире, ArcelorMittal и Tata Steel объявили о запуске по крайней мере одного такого рода проекта. А Китай, номер 1 по объёму производства, практически не начал работы в данном направлении.
Больше всего проблемой озаботились в Швеции. Там собираются вложить до 40 млрд долларов в «зеленые» разработки. На втором место идёт Южная Корея, а потом уже Германия. Однако есть надежды на то, что требования европейских правительств перейти к использованию «зеленых» государственных закупок простимулируют «озеленение» цепочек поставок в металлургическом сектора.
Повод для оптимизма
Несмотря на ограниченный прогресс сейчас в этой области, крупнейшие металлургические компании уже начали «озеленение» производственных процессов. В Бельгии ArcelorMittal внедряет установки улавливания отходящих доменных газов с высоким содержанием CO и CO2. Она преобразует их в этанол посредством процесса газовой ферментации с использованием микробов (проект Carbalyst). Вторая новация на бельгийских заводах — замена угля на древесные отходы. В итоге компания хочет запустить цикл производства биоэтанола.
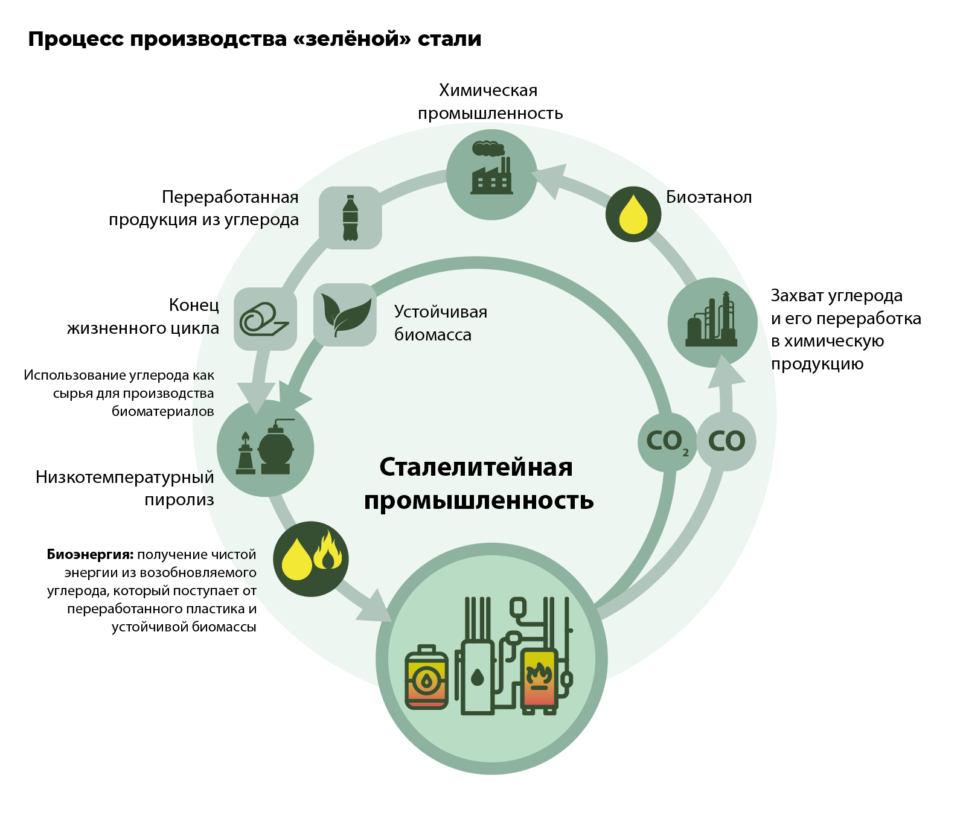
Японский производитель Kobe Steel в рамках перехода к технологии DRI начал внедрять технологию по добавке в доменную печь горячего брикетированного железа (железная руда с удаленным кислородом). Этот процесс снижает выбросы CO2, связанные с производством, примерно на 20 процентов.
В Нидерландах InnoEnergy совместно со шведской компанией Scania начали строительство завода, в котором вместо кокса при производстве стали будет использовать водород. При этом электроснабжение производства и получение Н2 будет производиться от возобновляемых источников. К 2024 году завод будет производить 5 миллионов метрических тонн зеленой стали, что сделает его крупнейшим заводом такого типа в мире.
Американский производитель Boston Metal, пользуясь поддержкой Билла Гейтса, собирается в течение трех лет запустить экспериментальный сталеплавильный завод, использующий технологию электролиза расплавленного оксида. В основе процесса лежит электрическое отделение кислорода от железной руды и выделение O2 в качестве побочного продукта вместо CO2. Такой установке не нужны будут технологии улавливания углерода, а перевод электроснабжения на ВИЭ по сути сделает его первым безуглеродным производством стали в мире.
Но это все — будущие проекты. Тем временем в августе 2021 года в Швеции удалось получить первую партию металла, изготовленную с использованием «зеленого» водорода по технологии HYBRIT. Теперь шведы собираются запустить полномасштабное промышленное производство «зеленой» стали к 2026 году.
А что же в России? В феврале 2022 у нас в стране приступили к сооружению завода по производству «зеленой» стали. Проект включает в себя строительство электрометаллургического комплекса полного цикла по экологичным технологиям и необходимой инфраструктуры в моногороде Выксе (Нижегородская область). Сталь будет производиться из железной руды с применением природного газа методом прямого восстановления железа (DRI). Объемы производства — 1,8 млн тонн стали в год. По проекту углеродная эмиссия должна будет сократиться в три раза по сравнению с аналогичным производством. Запуск планируется в 2025 году.
Успешный запуск и работа этого и предыдущих проектов по сути определит будущее всей отрасли на десятилетия вперед. Даже резкий рост цен на энергоносители вряд ли им помешает, так как это, наоборот, стимулирует максимально возможным образом сократить использование ископаемого топлива при производстве металла.
Водород — новое светлое будущее энергетики?